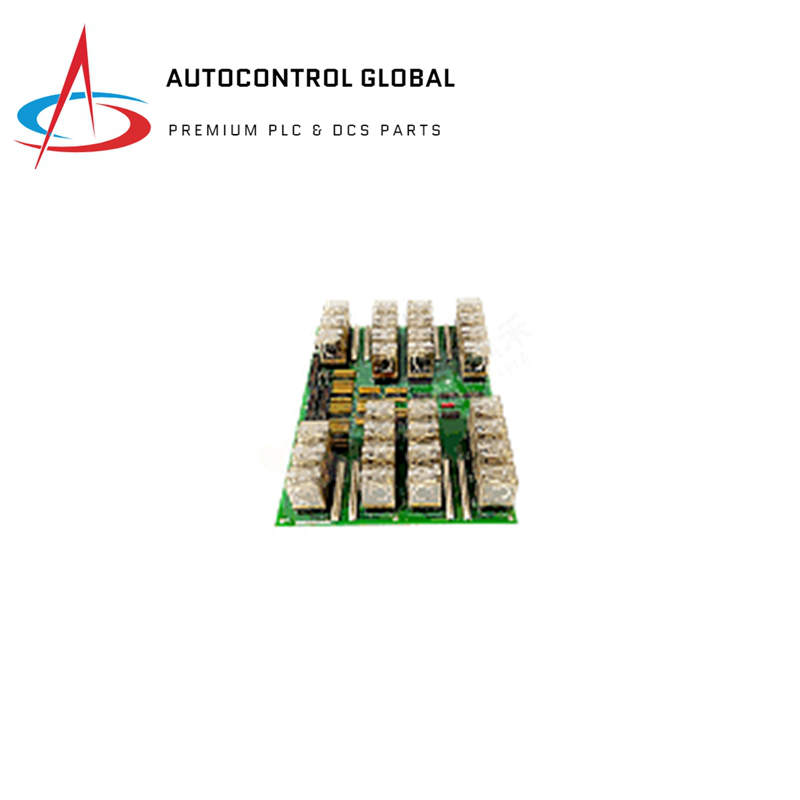
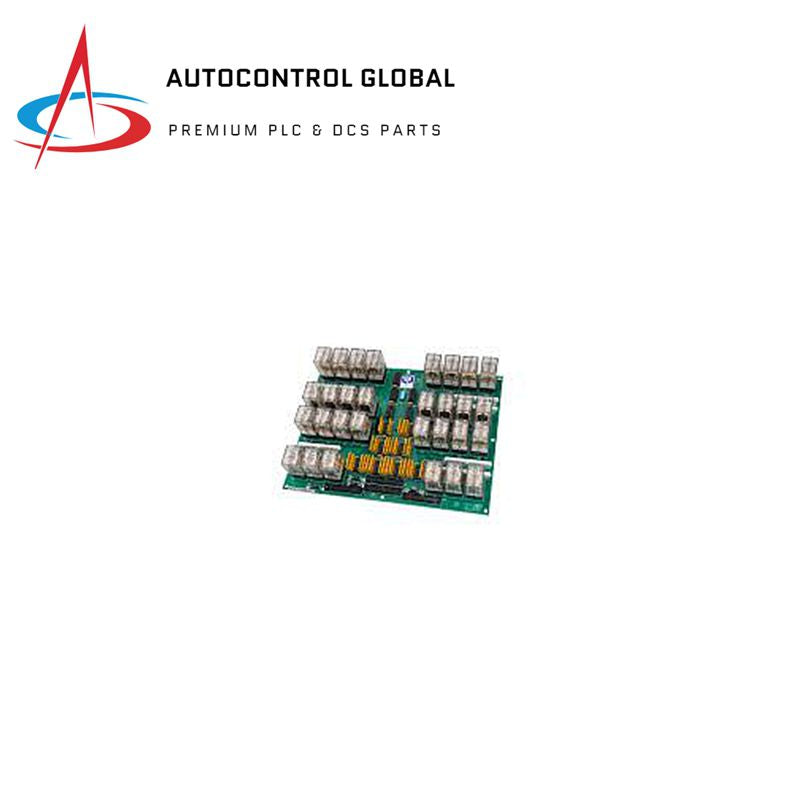
General Electric DS200TCRAG1ACC Relay Output Board
Manufacturer: GE Fanuc
-
Part Number: DS200TCRAG1ACC
Condition:New with Original Package
Product Type: Relay Output Board
-
Country of Origin: USA
Payment:T/T, Western Union
Shipping port: Xiamen
Warranty: 12 months
Technical Specifications
- Manufacturer: GE General Electric
- Series: Mark V
- Part Number: DS200TCRAG1ACC
- Functional Description: Relay Output Board
- Functional Acronym: TCRA
- PCB Coating: Normal Coating
- Revision Quantity: 3 Revisions
- Backwards-Compatibility: 1st two revisions
- Mark V Series Grouping: Group 1
About the DS200TCRAG1ACC
The DS200TCRAG1ACC is a printed circuit board (PCB) from General Electric, developed as part of the Mark V Turbine Control System Series. This series is used in the management and control systems of steam, wind, and gas turbine automated drive assemblies. The Mark V Series is considered a legacy series due to its manufacturing discontinuation. The DS200TCRAG1ACC is a Relay Output Board, a revised version of the original DS200TCRAG1, featuring three significant revisions. The Mark V Series is one of the final GE product series to use the patented Speedtronic control system technology introduced with the Mark I in the late 1960s.
Hardware Tips and Specifications
- Connectors: 4 34-pin connectors (IDs: JOR, JOS, JOT, JO) and 4 12-pin connectors (IDs: JS3, JS4, JS5, JS6)
- Relays: 30 plug-in relays
- Customization: Possible through the use of DTBC and DTBD optional printed circuit boards
- Relay Operation: Operated by signals from the CSP of the Mark V Series automated drive assembly
-
Installation Guidelines:
- Ensure knowledge of emergency shut-off devices and their operation
- Verify the area around the drive is clear and free of moisture or standing water
- Remove ungrounded two-prong power cords to avoid electric shock
- Inform operators and management of scheduled work to plan for disruptions
- Select a clear, flat, and sturdy workspace near the drive for installation